Subcontracting is a process where we order products from a vendor + we provide components to the vendor. This term must not be confused with “ Contract Manufacturing” where we directly order materials from the vendor without supplying any components.
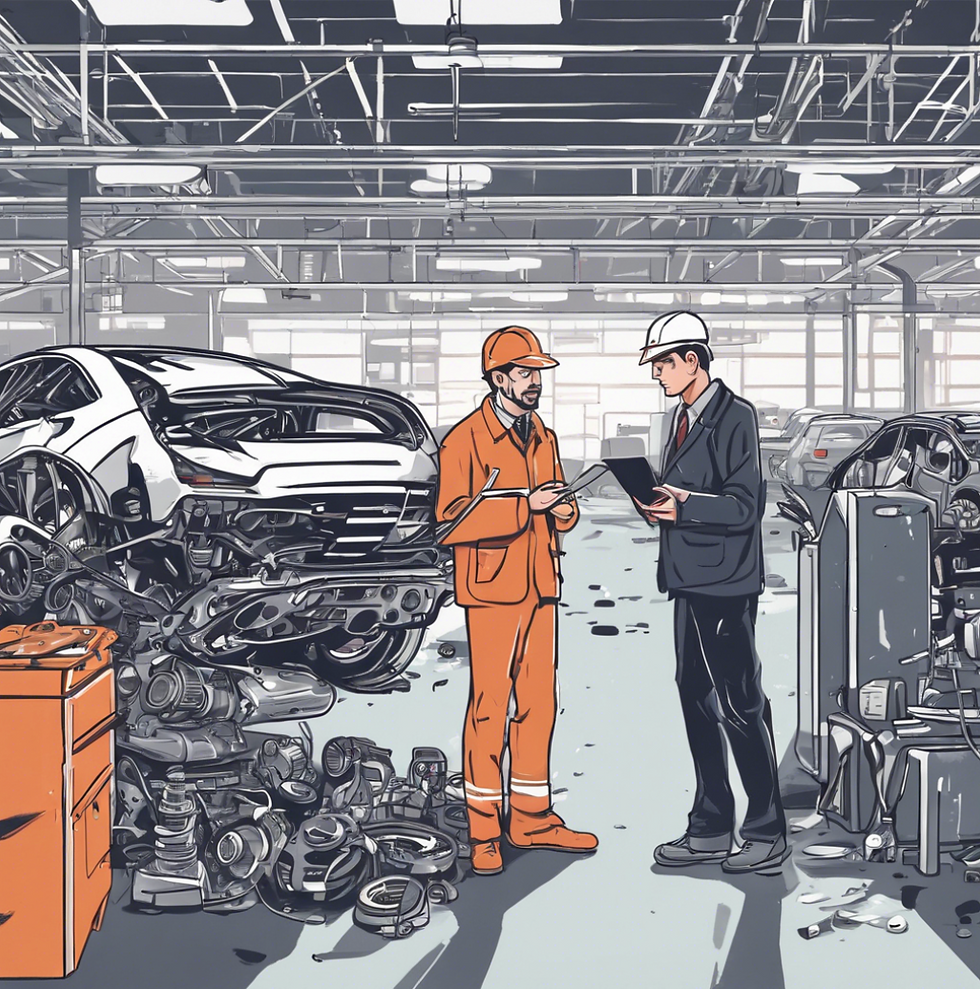
Subcontracting in SAP S4 HANA comes into the picture when we provide atleast one component (out of the total BOM components) to the vendor. It must be noted that Subcontracting PO is aServices PO as our vendor charges us a manufacturing service fee for the Finished Goods Production.We can provide one or more or all the BOM components to the vendor.
We create a SC PO to our vendor. The BOM components are copied from the BOM maintained by the purchasing department. Please remember, that the BOM Usage has to Purchasing or Universal. The component quantities in the PO can be edited by the buyer. Once the PO is checked and approved, it is sent to the vendor.
Generally, component inventory is maintained at the vendor premises as it would not make logistical sense to send components to the vendor everytime a SC PO is created. The components stock at the vendor can be monitored by Tcode ME20 or ME20N ( Subcontracting Cockpit ). Suppose there is insufficient component stock at the vendor, goods movements from the company to the vendor would be initiated by MIGO 541 Mvt Type or a 2 Step 30A + 30 C Mvt Type.
Once the delta component stock reaches the vendor premises, they can start the production
process. All ancillary components required for the process like screws and bolts will be used by the vendor and will be charged in the PO price.
Once the goods are shipped by the vendor, the company receives the ASNs ( shipping notification). When the goods arrive at the destination, the warehouse person executes PO based on the Inbound delivery number. SAP inwards the Finished goods with 101 Mvt Type and consumes the components by 543 Mvt Type. Any scrap component is inwarded by 545 Mvt Type.
The linkage of 101 to 543 is internally hard coded in the system and is not open to any manipulation. SAP makes the relevant accounting entries charging the GL accounts for Subcontracting.
Once the FG is received, SAP updates the inventory and consumes the component stock at a finance level. The components costs are debited to the inventory account based on the MAP prices maintained at the material master level.
If the vendor sends a notification that there is under / over consumption of components, we can book the differences by “ Subsequent Adjustment of Subcontracting Components”.
Stay tuned for a detailed post on Subcontracting Process rendition on a S4HANA server with all the transaction codes and accounting entries details.
Comments